CMC材料是由高强度的陶瓷纤维和陶瓷基体复合而成,在继承单相陶瓷耐高温的优点基础上,通过增韧机理设计,达到增加材料韧性的目的。在航空航天领域具有广泛的应用潜力。那么到底CMC材料有哪些特性及优势?如何制备?在航天航空的应用中面临着怎样的挑战? 以碳化硅陶瓷基复合材料(SiCf/SiC CMC)为例,通过在SiC陶瓷基体中引入SiC增强纤维,大幅度提高强度、改善脆性。CMC材料的结构和组织特征决定了其保留了碳化硅陶瓷材料耐高温、抗氧化、耐磨耗、密度小、耐腐蚀等优点,同时SiC纤维的增强增韧机制使得材料对裂纹不敏感,克服了陶瓷材料脆性大、可靠性差等致命弱点,从而成为各国重点研究的战略热结构材料。 
相比于镍基高温合金,CMC材料有以下显著优势: ● 比高温合金能承受更高的温度(CMC材料耐温极限比镍基高温合金提高约150K,可达1500K),可显著减少冷却气消耗量约15%~25%,从而提高发动机效率; ● CMC材料密度(2.0~2.5g/cm3)为高温合金的1/4~1/3,可以显著降低发动机重量(发动机减重30%~70%)从而大幅提高推重比; ● 高温下优异的持久强度; ● 可设计性强,纤维纺织技术的引入使CMC可设计性和结构适应性大幅提高,伴随着计算机CAE技术发展,CMC材料力学分析模型也向微-细-宏观多尺度发展,材料设计和结构设计耦合性提高,可根据不同部件的性能需求设计可达到最佳的热/力特性匹配。 鉴于优异的热/力学性能,CMC材料被视为军用/商用航空发动机核心机热端结构最理想的材料,广泛应用在航空发动机燃烧室内衬、燃烧室筒、涡轮叶片和涡轮壳环等热端部位,从而显著提高航空发动机性能。 目前,各航空强国普遍认为:CMC是航空发动机高温结构材料的关键核心技术之一,直接体现一个国家先进航空发动机和先进武器装备的设计和制造能力。作为航空发动机领域的技术制高点之一,对CMC材料研发重视程度和支持力度直接影响一个国家未来的航空动力发展水平。 经过多年的发展,CMC制备工艺已趋向成熟,目前主流的制备工艺包括以下三种:化学气相渗透(CVI),熔渗工艺(MI)和先驱体渗透裂解(PIP)。 ① 化学气相法 化学气相法用于制备Cf/SiC复合材料主要是化学气相渗透(CVI)和化学气相沉积(CVD)。但最常用的制备复合材料的方法是在化学气相沉积(CVD)的基础上开发的CVI。制备方法是将反应室纤维预制品封闭,采用蒸气渗透法,气相材料在加热纤维表面或附近产生化学反应,并沉积在纤维预制棒上,从而形成致密的复合材料。对于Cf/SiC复合材料的CVI制备工艺通常以三氯甲基硅烷(MTS)、四甲基硅烷(TMS)等为原料,H2为载气,Ar为稀释气体,高温下抽真空沉积SiC基体。 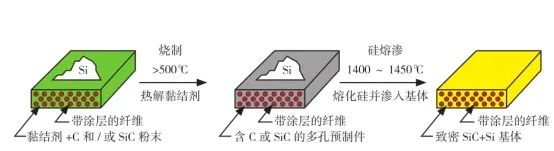
化学气相渗透(CVI) 化学气相法是在低于基体熔点的温度下制备合成陶瓷基体材料,因此纤维与基体材料之间不会发生高温化学反应,制备过程中对纤维损伤小,材料内部的残余应力小。通过改变工艺条件,能制备多种陶瓷材料,有利于材料的优化设计和多功能化。还能制备形状复杂、近净尺寸和纤维体积分数大的复合材料。 但随着渗透的进行,孔隙会变小,渗透速度也就变慢,因此生产周期长,设备复杂,制备成本高;制成品孔隙率大,材料致密度低,从而影响复合材料的性能;因此不适于制备厚壁部件。 ② 熔渗法 熔渗工艺(MI)是在反应烧结SiC基础上发展起来的复合材料制备工艺,根据熔渗过程中是否存在碳与硅的反应,可分为反应熔渗(RMI)和非反应熔渗(MI)两种。其基本工艺流程是:利用CVI工艺在SiC纤维表面沉积涂层(界面相);在纤维涂层表面继续沉积一定厚度(约3-5μm)的SiC基体;引入陶瓷浆料;硅或硅合金液相熔渗(或反应熔渗)。 
CMC的熔渗工艺 MI工艺是一种低成本、快速致密化工艺,工艺简单,周期短,制备的复合材料几乎无残留开气孔,具有非常高的热导率和气密性,气孔率低于2%。利用MI工艺成功开发的C/C-SiC,C/SiC和SiC/SiC等复合材料,已应用到航空航天、摩擦刹车系统中。 ③ 先驱体转化法 先驱体转化法又称先驱体裂解法或聚合物浸渍裂解法(PIP法),是近年来发展迅速的一种Cf/SiC复合材料制备工艺,由于成型工艺简单、制备温度较低等特点而受到关注。先驱体转化法是利用有机先驱体在高温下裂解进而转化为无机陶瓷基体的一种方法。 该工艺制备碳纤维增强复合材料的基本流程为:将含Si的有机聚合物先驱体(如聚碳硅烷、聚甲基硅烷等)溶液或熔融体浸渍到碳纤维预制体中,干燥固化后在惰性气体保护下高温裂解,得到SiC基体,并通过多次浸渍裂解处理,获得致密度较高的复合材料。与溶胶凝胶法不同的是,先驱体转化法主要用于非氧化物陶瓷,目前以碳化物和氮化物为主。 
CMC的PIP工艺 运用先驱体转化法在聚合物中浸渍,能得到组成均匀的陶瓷基体,具有较高的陶瓷转化率;预制件中没有基体粉末,因而纤维不会受到机械损伤;裂解温度较低,无压烧成,因而可减轻纤维的损伤和纤维与基体间的化学反应;陶瓷基体可设计性强、易于通过近净尺寸成型实现大型复杂构件的制造。但该工艺的致密周期较长,制品的孔隙率较高,对材料蠕变性能有一定影响;基体密度在裂解前后相差很大,致使基体的体积收缩很大(可达50~70%)。 现阶段CVI法和MI法都已实现大规模工业化生产,PIP法制备大型结部件也逐步达到实用化水平,能够显著提高生产效率,但这3种制备工艺由其工作原理导致均存在显著的局限性,因此在制备结部件时应根据热-力学特征选择相应的制备工艺。对于某些特殊要求的应用领域,CMC的制备不限于某一种制备工艺,可同时结合多种制备方法以满足部件的设计要求。 尽管CMC材料具有诸多显著的优点,但在实际应用,特别是热分析方面也存在巨大挑战。根据CMC材料构成可知,增强纤维和基体之间的强度和导热系数存在显著差异,并且纤维布置的方向性导致了CMC材料强度和导热系数呈现出显著的各向异性,从而影响结部件的力学和传热特性。这种由于内部非均质的结构特征并且纤维的轴向与径向的导热系数相差较大,从而使材料导热系数具有明显的各向异性,是纤维增韧复合材料的共性。导热各向异性特性使CMC材料的热分析与高温金属截然不同,因此基于CMC材料的航空发动机热端部件设计需要充分考虑各向异性导热特性带来的挑战。 
涡轮尺度CMC编织结构及其各向异性热传导 CMC的导热特性是CMC部件热分析的关键影响因素,另外其编织方式决定其导热特性,目前的CMC制备技术有多种编织方式,导致其各向异性导热系数的分析方法也不同。CMC根据纤维编织方式可分为3类:(1)单向纤维增韧复合材料,其制备和加工制造简单,但抗剪切能力弱;(2)2维/2.5维纤维编织CMC,抗剪切能力相比于单向纤维增韧复合材料有大幅提升,但加工和制造难度增大;(3)3维纤维编织CMC材料,具有优异的机械性能被广泛应用于航空航天的耐高温部件,其制备工艺和加工制造技术难度大。
|